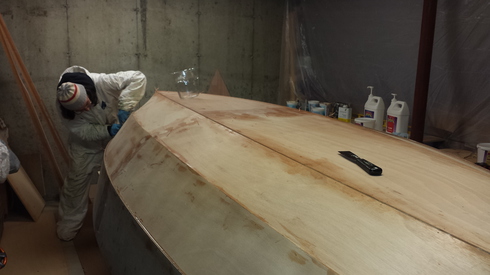
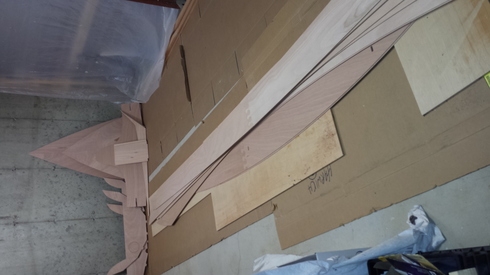
This morning the basement was warm enough for us to consider doing the next step, which is to use two different mixtures of epoxy to "tack" the bottom and planks together. This sets the boat up for the next step of removing all the wire ties.
We are building a small boat in our basement. Not rushing, we have all winter to do it. Yes, we lifted the boat the other day and worked it around and into the doorway out of the basement. Plan A... check Plan A...
Lots of anticipation and quite a storm it was. The run-up on the Weather Channel was good and we watched intently. Went out the day before for a look-see. Then, back out the next day to have another look. A couple of pictures.
We've been sitting around all weekend, since Norm had a sore back. Bending over the skerry stitching, as attractive as that is, was not in the cards for Norm. We did check out the wind at our favorite spots on Saturday.
Today we did the second sanding on the finger joints. Things look pretty good there. Mostly smooth. As we were sanding, we started to notice these little holes close to the edges we would be stitching. Hmmm. Had Chesapeake Light Craft pre-drilled all the holes? Well, yes they did! How nice :)
After the epoxy was set from Day 5, we removed all the wax paper. You can tell the epoxy is set since it is not tacky. There were a few low spots and gaps in our joints, so we mixed another batch of thickened epoxy and put a second coat on each surface. You could tell that we got better at the spread and squeegee in our first round. The first few joints were rougher and had more gaps than the last group. So another hour playing with goop, and then wax paper separations and leave it to dry.
Today started out at 18 degrees, and the basement was pretty cold. We thought perhaps we would not be able to do any epoxy, but by this afternoon, the temp outside had warmed up to 38 and there was a light snow falling. Very pretty!
Norm spent this day lightly sanding the finger joints on each piece. We wanted to make sure there was enough room in the joints for the thickened epoxy. After sanding he dry fit all the pieces again. Ready for epoxy tomorrow.
Today Norm and I prepared the space in the basement. We set aside enough room to accommodate the 15 feet length and 4 1/2 ft width of the boat. Plus some work tables to hold things like wire and epoxy and clamps. Norm sealed off the space with drop cloths, so we can try to bring the temperature up to somewhere above 60 degrees. This way the curing time will not take forever. Maybe twice as long as a 70 degree workspace.
Two of the grandkids are reading Swallows and Amazons, and their imaginations are firing on all cylinders. Norm found a kit for building a skerry, at Chesapeake Light Craft Company. We ordered it to arrive just after Christmas, with pictures of the boat sent to the grandkids for their Christmas Stockings. The boat arrived January 6 around noonish.